-
Assessment of Companies
-
Key commercially relevant patent filings and public technical statements are discussed in the company chapters below,
which results in a projection by the author in the form of industrially plausible manufacturing processes that could
allow for the synthesis of novel Si-based active materials (prospective active material characteristics are also listed).
-
In the following chapters, patent families that were not covered in the prior review edition (February 2022) are shown in red.
-
Author comments are displayed in maroon.
-
Example of Company Chapter – Umicore – Belgium
Version: 2024-08-30
-
Organization Profile
Umicore
(http://www.umicore.com)
is a market-leading supplier of NMC cathode materials that is also active in transition metal recycling.
Unique capability: Si-carbon composite formation process that involves RF-ICP (radio frequency inductively coupled plasma).
Leap of faith: manufacturing can be upscaled quickly and cost-effectively as claimed (presumably involving RF-ICP-based Si volatilization and
formation of Si nanoparticles), achieving a sufficiently small Si particle size to achieve sufficient cycling stability.
To the extent of the author’s knowledge, RF-ICP is not used at current to commercially produce materials used in the Li-ion battery industry.
Thermal plasma gasification plants with >500 tons per day have been built to treat municipal solid waste,
which might be considered as industrial scale validation of a related process in a comparably cost-sensitive application (waste disposal).
Key differences as compared to 2022
-
Umicore announced its plans
“to be the 1st European silicon anode player at scale”.
-
According to a patent portfolio analysis, Umicore might target an anode material with well-rounded performance by incorporating RF-ICP
volatilization and deposition of Si nanoparticles into a sulfur-containing carbon matrix (no use of monosilane gas).
Possible composition of future silicon-based negative electrode active materials
(for liquid carbonate-based, semi-solid or solid electrolyte cells):
-
According to a SEM image from a
presentation at The Battery Show Europe 2023 (slide 11),
the active material appears to consist of microparticles that contain homogeneously mixed Si-carbon nano-domains (without or with a small volume of void space), mixed with graphite flakes.
- BET SSA of 4.8 m2/g (might be further reduced by applying a carbon or polymer coating, although no recent patent literature was identified in this regard).
- Si / O / S / C mass ratio of 40.1 : 3.4 : 0.109 : 56.4.
-
Particle size distribution of Si nanoparticles: dNS10 = 59 nm, dNS50 = 114 nm, dNS90 = 192 nm.
Presumably, the evolution towards higher capacity and Si content in Si-carbon composites goes along with further reducing Si nanoparticle size.
- Oxygen content of Si nanoparticles: 7.8 mass%.
Figure U1: projected manufacturing process for Si-carbon composite active material by Umicore (red: changes vs. 2022 review edition,
up-scaled implementation may vary)
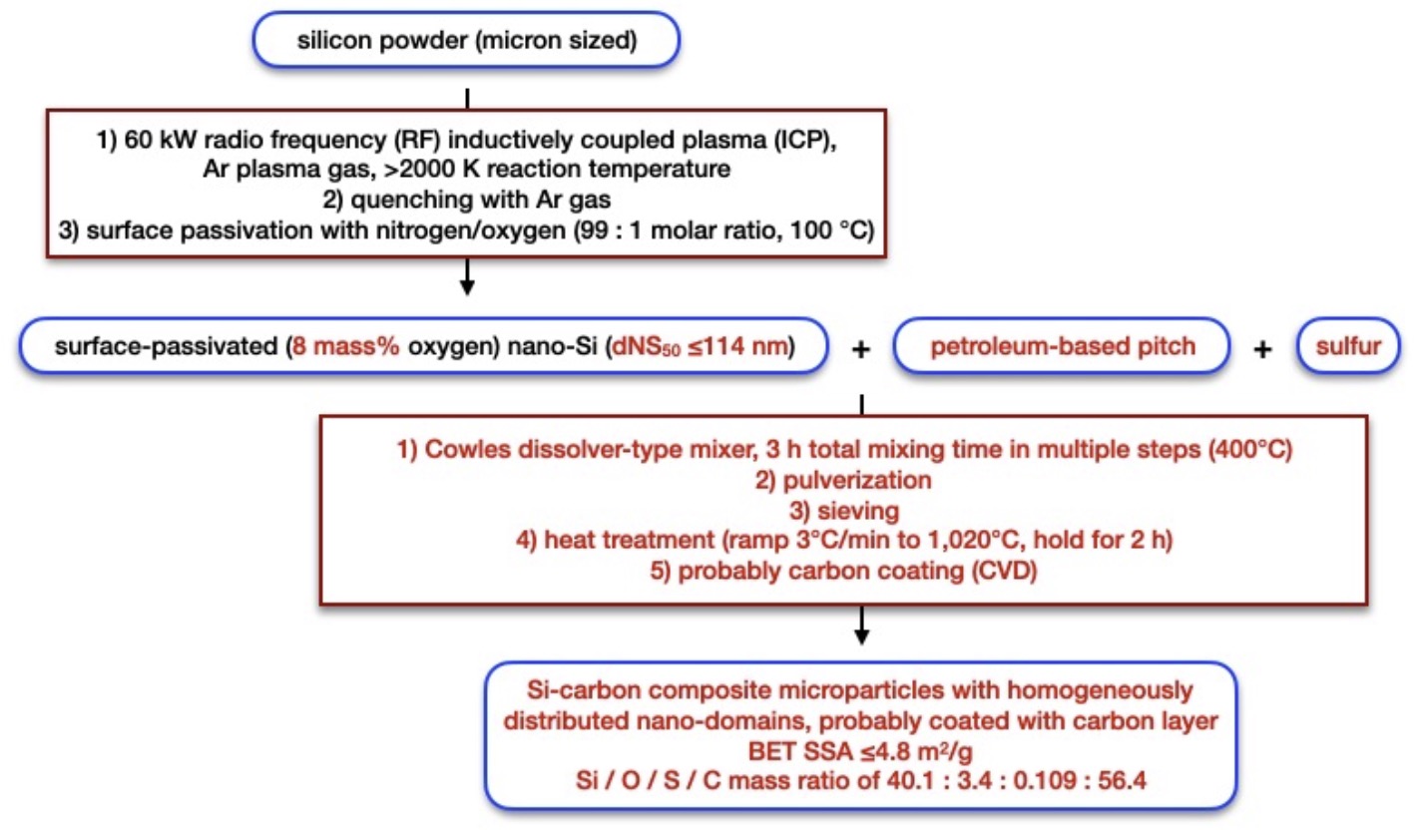
Public technical statements & reports
At The Battery Show Europe in June 2023, Jean-Sébastien Bridel (Anode Program Manager) stated:
- Their target is to become the first European silicon anode player at scale.
- By 2029, Si-carbon composite active materials will supersede SiOX in terms of volumes deployed in cells.
- They are in the process of launching Si-carbon composite materials that are not produced from silane gas.
- In terms of the IP landscape, freedom of operation is higher in the area of Si-carbon composites as compared to SiOX (control of key IP by a few major players).
- They have an anode-related IP portfolio with 39 patent families (over 200 patents).
- Several EV customers (battery makers and OEMs) confirmed the favorable and well-balanced performance of their Si-carbon active material (active material is being delivered to these customers at ton-scale).
- They achieve the best costs (USD/kWh) upon use of abundant raw materials, and can scale up their process based on easy equipment access.
- Their UM1500XX and UM1650XX grades exhibit capacities of 1,500-1,650 mAh/g.
-
Their UM1300MG grade exhibits a capacity of ≈1,300 mAh/g and a capacity retention of ≈87% after 1,000 cycles
(1 C charge / discharge, NMC811-based positive electrodes). An SEM image after cycling (slide 11)
suggests that Si-carbon composite microparticles remained intact, inside which Si and carbon
nanodomains appear to be homogeneously distributed. Favorable stability due to an engineered
Si-carbon interface and Si volume change compensation by the carbon matrix are claimed.
- Their Si material does not undergo a phase change during cycling.
- No pre-lithiation is necessary.
General patent portfolio characteristics
7 new patent families by Umicore have been published since 2022 that are related to high-energy Li-ion battery anodes (without lithium metal anodes).
3 new lithium metal anode patent families have been published since 2022.
Example from the patent portfolio
Active materials – A) chemical composition; B) nano- & micro-architectures, composites; C) surfaces & coatings
-
Process in Figure U1 –
A POWDER FOR USE IN THE NEGATIVE ELECTRODE OF A BATTERY, A METHOD FOR PREPARING SUCH A POWDER AND A BATTERY COMPRISING SUCH A POWDER
(published in 2023, covered in patent update):
micron-sized silicon powder was injected into an RF-ICP (200 g/h, 60 kW, reaction temperature >2,000 K), which resulted in complete vaporization,
followed by deposition in an argon gas flow (20 Nm3/h, <1,600 K), followed by a passivation step
(100°C, 5 min, 100 L /h, N2 /O2 = 99 : 1 molar ratio).
The resulting material exhibits a BET SSA of 81 m2/g, an oxygen content of 7.8 mass%,
and a number-based particle distribution of dNS10 = 59 nm, dNS50 = 114 nm, dNS90 = 192 nm.
This powder was blended with petroleum-based pitch powder and sulfur (100 : 200 : 0.45 by mass, 400°C, under nitrogen, Cowles dissolver-type mixer,
3 h total mixing time in multiple steps), followed by pulverization, sieving, a heat treatment (heat at 3°C/min to 1,020°C, hold for 2 h),
sieving.
The resulting material exhibits a BET SSA of 4.8 m2/g, an Si / O / S / C mass ratio of 40.1 : 3.4 : 0.109 : 56.4 and a first cycle
discharge capacity of 1,342 mAh/g. Negative electrodes in which graphite active material was additionally included exhibit a 1st
cycle discharge capacity of 847 mAh/g, a coulombic efficiency of 90.73%, and an average coulombic efficiency in cycles 5-50 of 99.79%
(half-cells), as compared to 846 mAh/g, 89.31% and 99.64% for a comparative example with an active material that was prepared without sulfur.
Additional, earlier patent families follow a similar RF-ICP-based approach to obtain Si nanoparticles, while relying on different carbon
precursors that apparently led to worse electrochemical performance as compared to the approach discussed above:
- WO 2022074031 A1: use of petroleum-based pitch without sulfur.
- WO 2023275223 A1: use of phenol-formaldehyde resin without sulfur.
This work illustrates how the presence of a minor amount of sulfur improves the electrochemical characteristics of Si-carbon composite materials.
This patent filing could plausibly cover the active material presented at Battery Show Europe 2023 (see above),
although there is no absolute guarantee that this is the case.
-
Key earlier patent that might correspond to prospective commercial products
Active materials – B) nano- & micro-architectures, composites; C) surfaces & coatings
-
Process in Figure U1 –
A POWDER FOR USE IN THE NEGATIVE ELECTRODE OF A BATTERY, A METHOD FOR PREPARING SUCH A POWDER AND A BATTERY COMPRISING SUCH A POWDER
(published in 2021, covered in patent update, granted by CN): a sub-micron silicon powder (d90 : 205 nm)
was synthesized by applying 60 kW RF-ICP to a micron-sized
silicon powder (argon as plasma and quenching gas, >2,000 K reaction temperature). In a passivation step, the powder was treated with a nitrogen / oxygen mixture
(1 mol% oxygen, 100°C). This powder was mixed with zirconium powder (average particle size 50-100 nm) and ball-milled under argon, followed by a heat treatment
(773 K, 2 h, dry argon, <3 ppm water, <3 ppm oxygen). Oxygen content in product particles: 8.7 mass%, Zr content: 0.1-5 mass%, BET SSA: about 83 m2/g.
Using an XPS analysis, the oxidation state of Zr near the surface (up to 10 nm depth) was confirmed to be +IV. It is unexpected that a 1st cycle efficiency
of 88.15% is reported in consideration of the high surface area of the Si particles and that 25 mass% carbon black were used in negative electrodes along
with 2 mass% carbon fibers and 25 mass% PVDF.
This work suggests that a ZrO2 coating of Si nanoparticles results in a favorable electrolyte / electrode interface in cells.
-
32 additional company assessments are included in the full review.
|